STV’s design for the third phase of the Pennsylvania Department of Transportation’s (PennDOT) Betsy Ross Interchange (BRI) Reconstruction project included a three-level interchange appointed with several ramps. During the design phase, the ramps challenged our team by providing significant site constraints: they crossed over multiple passenger and freight rail lines, electric transmission lines, a maintenance yard, and a neighboring creek, to name a few.
The complex site conditions were ideal for PennDOT to pilot the nation’s first steel curved tubular flange girder. With PennDOT’s initiative and our project team’s ability to innovate, STV was up to the challenge.
Curved tubular flange girders have benefits over traditional curved I-girders both in design and construction. Design advantages include increased torsional stiffness and lateral-torsional stability, and increased web stability. All of these benefits lead to overall weight savings of the girder section, the ability to minimize under clearance, simplifying erection, and eliminating cross frames or diaphragms. For the BRI project, the main benefit was the ability to use a single crane while navigating the numerous site constraints.
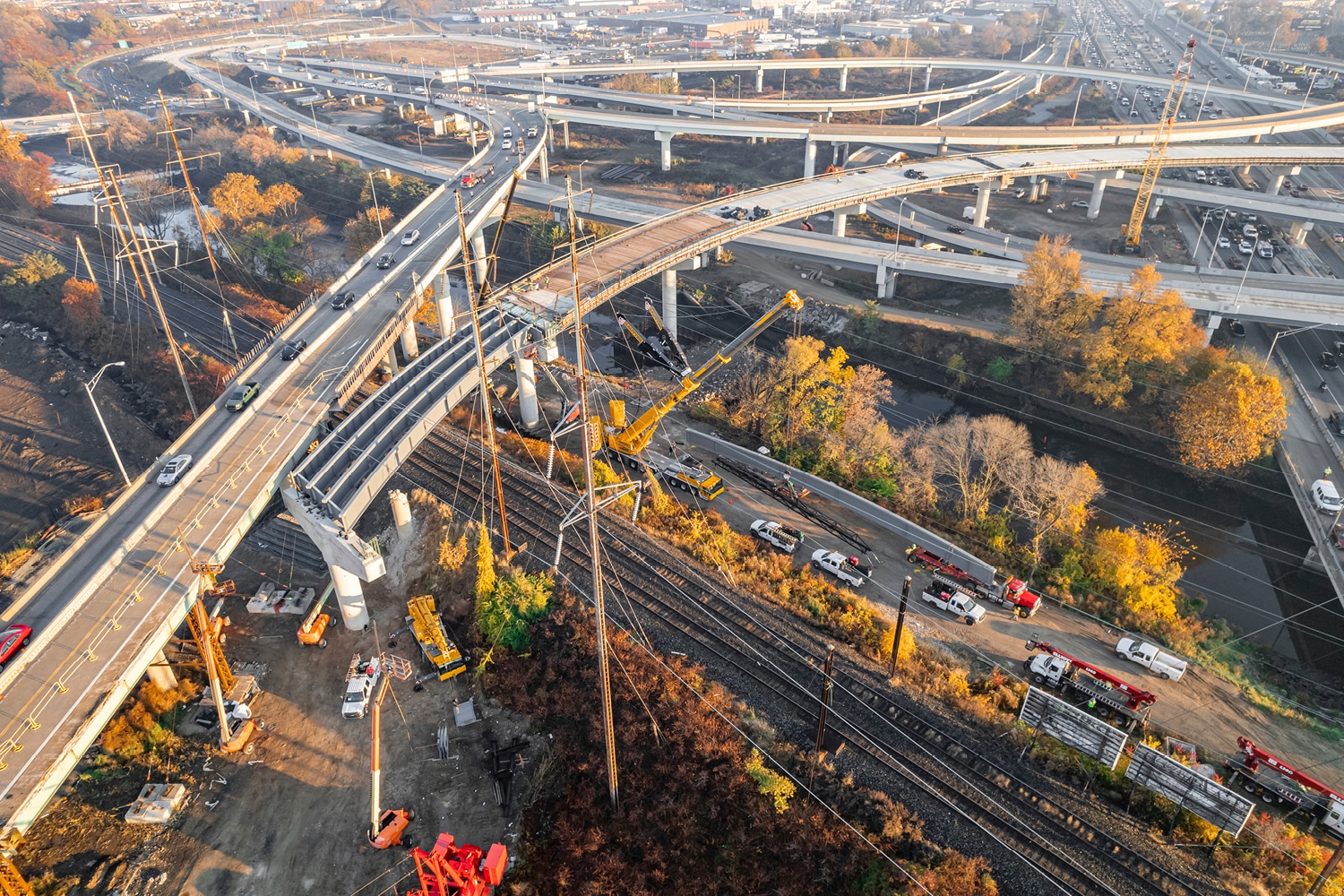
The tubular flange girder concept was developed by Dr. Richard Sause of Lehigh University, and the idea for this application originated with Tom Macioce when he was the PennDOT Chief Bridge Engineer.
Through PennDOT-funded research, the first tubular flange girder bridge was built in 2010. For the BRI project, STV worked in conjunction with Dr. Sause to extend the concept to a curved girder bridge which capitalizes on the tubular flange benefits.
With a standard I-girder, a project team designs with the lateral forces (traffic, wind, etc.) in mind. But for a curved ramp that passed over the freight rail line (like Ramp B on I-95), we also had to consider the centrifugal force, lateral bending of the structure, and the natural resistance any straight, standard girder would have when being shoehorned into a curved ramp. The less resistance to those forces and loadings, the better: a curved design was ideal.
In short, use of a tubular flange increases structural performance while reducing fabrication and erection material, as well as erection time.
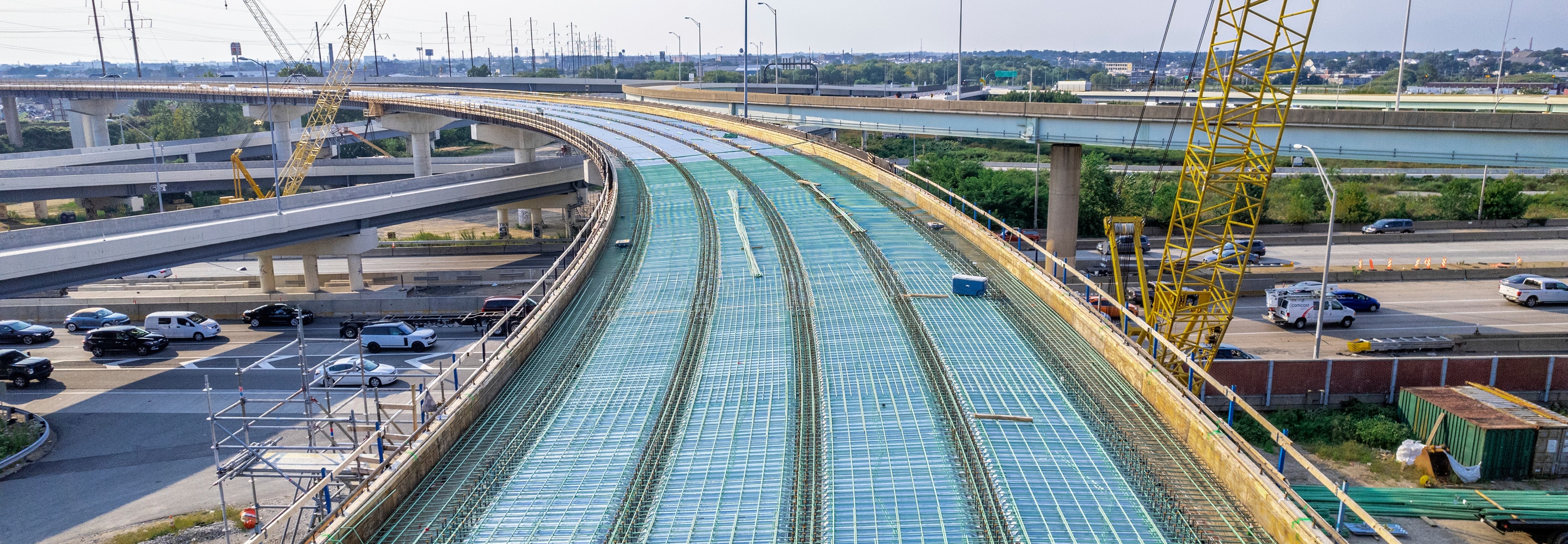
Working closely with PennDOT’s Henry Burman, P.E. and civil engineer, and with Quality Assurance support from the original concept researchers at Lehigh University, STV had a strong team to support fabrication and oversight.
The firm was heavily involved in the fabrication, modeling, and testing of the steel for this first-of-its-kind construction. The firm’s structural lead, Justin Eberhart, P.E., CBSI, used a handheld 3-D imaging to check and measure the tubes for distortions, and detailed equations to meet the needs of the curved components.
When the time came to erect the ramp, the beams were delivered below the bridge via a nearby access road with a 500-ton crane. Typically, two cranes are used for lifting curved girders – a dual approach called “sistering.” But working within a 550-foot radius, the project team looked again for creative solutions.
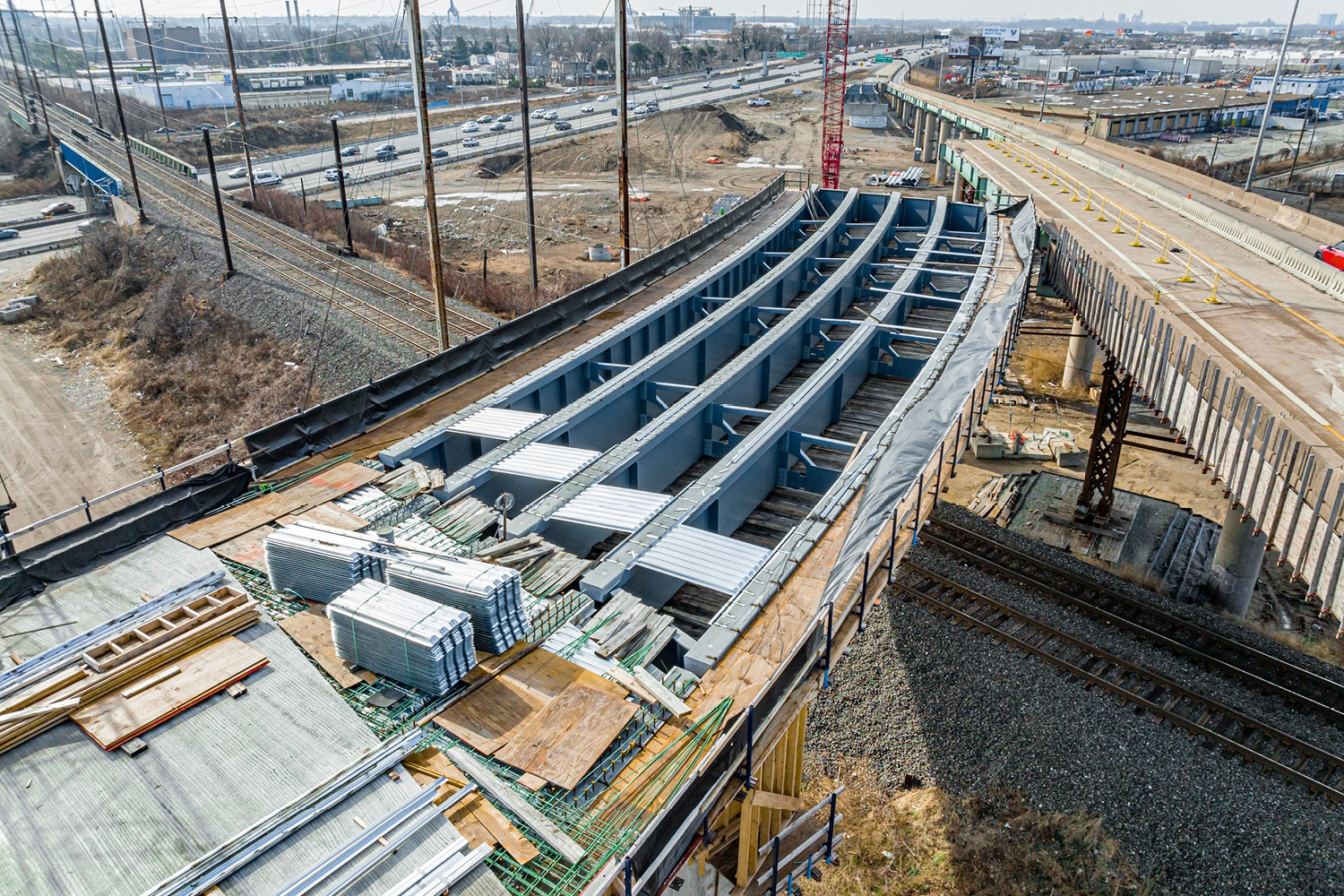
In the end, the project team used 150-foot-long temporary supports off each pier to support the girder, so the components could be installed with just one crane. This meant interruptions to transmission lines could be staggered, and traffic in the opposite direction could continue.
With the construction of this segment estimated to conclude next year, it’s an honor for STV and our bridge practice to be able to share the successes of PennDOT’s pilot as the project’s lead designer.
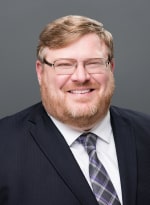
Geoffrey Stryker, P.E., is a senior project manager in Harrisburg. He has more than 20 years of experience planning and designing transportation and infrastructure improvements for public and private partners throughout the northeast. His expertise includes bridge replacements, rehabilitations, preservations; and large-scale highway improvements.