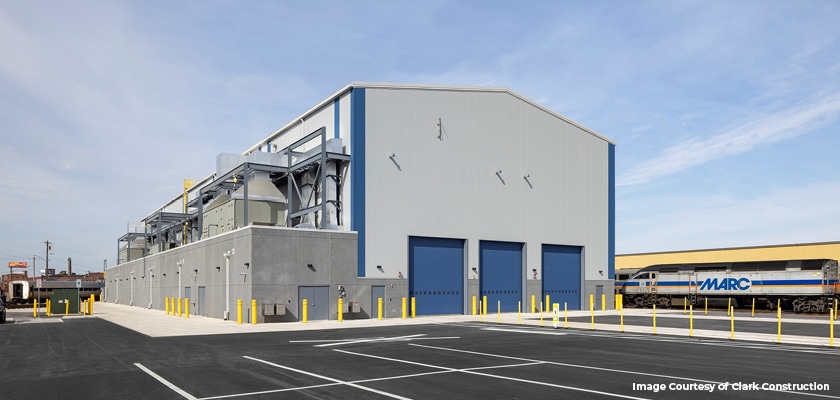
Maintenance facilities are often large and imposing, with a function that focuses primarily on industrial processes. Designed for machinery, automation and efficiency, they can seem oversized and overpowering to the human scale.
The recently completed MARC (Maryland Area Regional Commuter) Riverside Heavy Maintenance Facility breaks this trend, exemplifying a human-centric approach to designing large-scale industrial facilities. Located in Baltimore, MD, this 32,113-square-foot facility was designed to support maintenance functions for MARC’s new Siemens Charger rail cars, calling for high spatial clearance and specialized industrial equipment unavailable in existing facilities.
STV served as the lead designer for the $48.3 million construction management-at-risk (CMAR) project, providing design and construction administration; architecture; site/civil; utility relocation; stormwater management; structural; industrial; mechanical, electrical, and plumbing; communications; landscape architecture; geotechnical; hazardous waste removal; and corrosion control services.
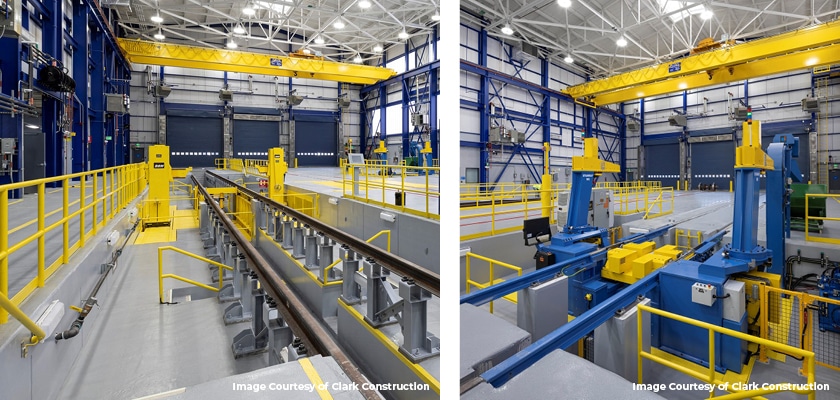
At its core, the facility was designed to incorporate three major industrial components: a wheel truing machine, a drop table machine, and a 30-ton overhead crane. A customized structural steel framing, rather than a pre-engineered structure, allowed for flexibility in accommodating this equipment as well as high spatial clearance requirements.
Another important design goal was the integration of durable and long-lasting materials to ensure a sufficient building lifespan. Finally, a major challenge of this project was the need to deliver it within a limited budget and a short construction schedule of 24 months.
Still, despite the emphasis on complex industrial needs, the MARC Riverside Facility prioritized a human-centric design. In addition to optimizing maintenance processes, the design incorporated features that catered to the experience and well-being of the workers who would be using the facility.
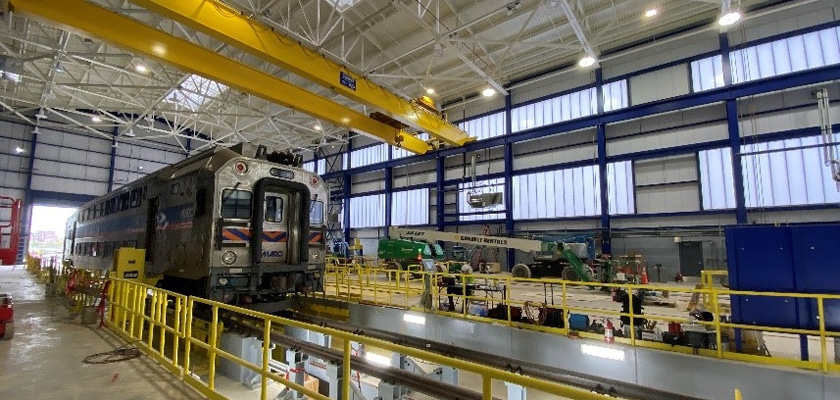
Windows are notoriously absent in maintenance facilities due to prevalent concerns about glare. Yet, an essential element for creating a positive and uplifting work environment, STV incorporated daylighting into the design. Through a comprehensive lighting and glare analysis, the team was able to ensure that maintenance activities would not be impeded. Double-walled polycarbonate glazed windows and skylights were chosen to provide ample illumination without causing glare.
To allow for continuous 24-hour operations, the double-walled system ensures that maintenance on the glazing could be performed on one layer at a time. STV also carefully balanced natural and electrical lighting to maintain uniform lighting throughout the day. Utilizing energy-efficient LED lamps, the consistent lighting conditions enhance both comfort and productivity for workers. The lighting design was centered around the needs of the human experience inside the building, while always accounting for operational requirements.
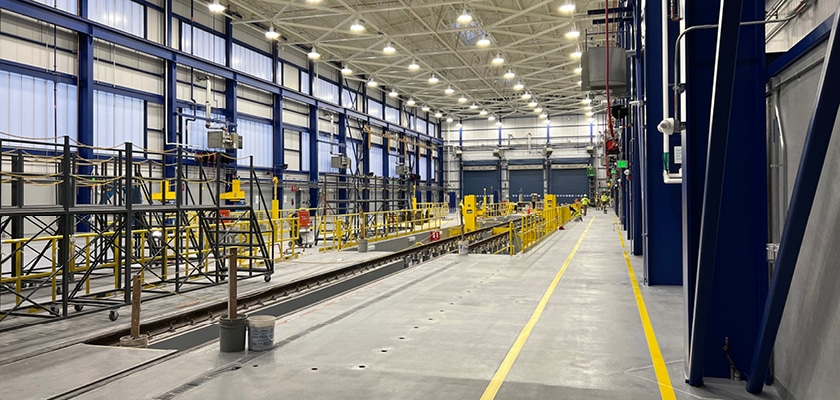
Flooring, often overlooked in maintenance facilities, was carefully considered to provide a more comfortable work environment. Instead of plain concrete floors, the facility incorporated a resinous flooring system with epoxy topcoat. This choice improves comfort, impact resistance, chemical resistance, and slip resistance for staff.
Ventilation was another crucial aspect of the facility’s design due to the high fumes and gas emissions from diesel locomotives. Special attention was given to controlling nitrogen dioxide (NO2) and carbon dioxide (CO2) levels within the building to ensure optimal air quality and comfort for workers. Air curtains were installed at the entrance of each overhead door to minimize the influx of exhaust air when doors are open.
The appropriate level of air handling was achieved through an innovative mechanical design decision that played a vital role in maximizing space utilization within the facility. Addressing space constraints, STV placed a significant amount of dedicated outdoor air system (DOAS) equipment on the lower roof of the building. A low-slope modified-bitumen roof system was employed to house the mechanical equipment, eliminating the need for a separate dunnage structure. This approach led to both space and cost savings while providing the necessary ventilation to ensure a comfortable and healthy work environment.
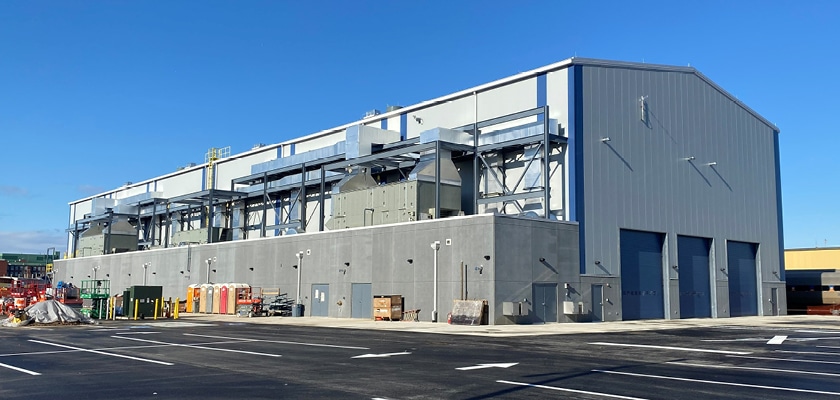
High-quality, durable, and long-lasting materials and finishes were carefully chosen to achieve a modern, aesthetically pleasing facility with an extended lifespan. Insulated precast concrete panels provide durability around the lower portion of the building. At the higher elevations, insulated metal panels form the wall system. High-performance coatings cover interior steel and walls, while a three-coat Kynar system wraps the exterior metal panels.
Sustainability was another consideration, with a focus on recycled and locally sourced materials. The light exterior façade and metal roof delivered high solar reflectance index (SRI) values to minimize heat island effects. Energy consumption was reduced through daylighting and LED lighting, as well as a minimized need for heating and cooling through the strategic segregation of different functional areas.
Collaboration with the client played a crucial role in maximizing the facility’s human-centric focus. Throughout the design process, the Maryland Department of Transportation Maryland Transit Administration (MDOT MTA) provided valuable insights and feedback, resulting in a facility that aligns perfectly with MARC’s operating requirements while prioritizing a worker-friendly environment for maintenance staff.
The MARC Riverside Facility stands as a role model for future MDOT MTA facilities. It showcases the integration of human-focused design principles in large-scale, complex industrial projects, setting a new standard for functional, people-oriented spaces in the industrial sector.