With the recent passage of the Senate Commerce Committee’s bipartisan Federal Aviation Administration’s (FAA) Reauthorization Act , the spotlight on aviation safety and customer experience has new momentum.
As our nation’s airport owners and operators upgrade and modernize their facilities, it is also imperative that these hubs continue to serve our passengers and communities. STV, a leader in aviation, with more than 30 years of Construction Management (CM) service on behalf of our clients and other related stakeholders, has helped facilitate the vital improvements that are reshaping airport infrastructure in some of the nation’s busiest cities as stakeholders strive to uphold the standards set forth by regulatory authorities.
In this CM roundtable, Rigo Salinas, senior vice president and national development director for the firm’s CM operating group talks with his STV colleagues and reflects on the nuanced way the team provides a full array of planning, multi-disciplinary design, advisory and CM services that enable our aviation clients to meet strict deadlines and tight budgets, all while striving to maintain crucial airport operations throughout construction.
Rigo Salinas: When a new terminal opens, as passengers we’re often drawn to the most apparent customer experience elements like cosmetic upgrades and enhanced screening and security checkpoints. What are some of the unseen changes that impact travelers?
Jonathan Clouser: I’ve been fortunate to work on one airport improvement program for over a decade, so I’ve seen the transition from complete gut renovation to the polished end result. With each upgrade a customer sees, there are so many changes behind the scenes. For example, with the removal and replacement of all passenger boarding bridges at LaGuardia Airport, we were able to scan existing Mechanical, Electrical, and Plumbing (MEP) utilities at night and create a model that we could then hand off to the contractors as a building block to determine the most efficient method to remove and replace the systems.
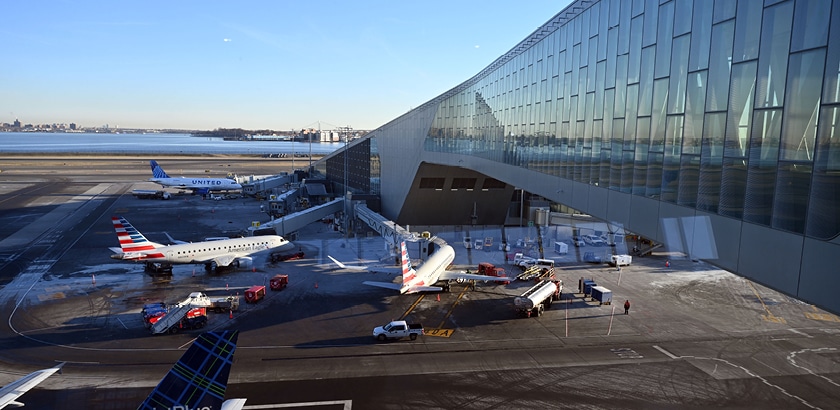
From there, we architecturally split the concourse that was under construction between what was occupied and operating versus areas actively undere construction. Each region had different HVAC zones, with dedicated fire protection that proceeded without interruption. To accomplish that, we set up temporary loops of piping, which eventually were incorporated into the final design – ultimately minimizing cost to the client and impact to the customer.
Patrick McCollom: For several airport projects in New York City and Houston we also had to incorporate contingency planning for seismic activity and flooding following Superstorm Sandy in New York and Hurricane Harvey in Texas. These contingencies include flood control devices and updates to elevation requirements.
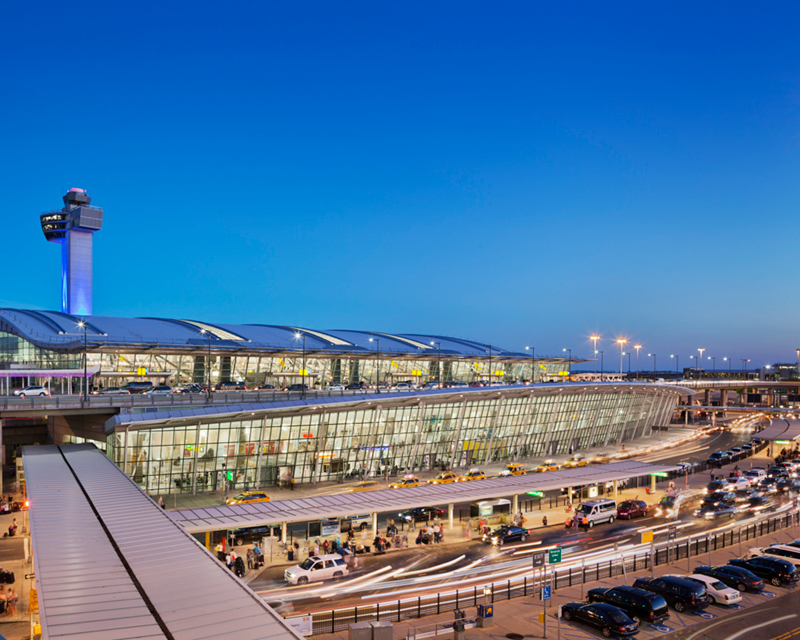
Rigo Salinas: With complex logistics and phasing like this, how do you manage the project budget and incorporate contingencies?
Cory Leonard: One of the main roles of project controls is to provide scalable processes and procedures specific to costs and schedule management – all of which must be developed to not only meet the requirements of the owner/client but also to ensure the contractual obligations of the supply chain are met.
Lawrence Pitkin: I’d describe it as cooking Thanksgiving dinner while remodeling the kitchen.
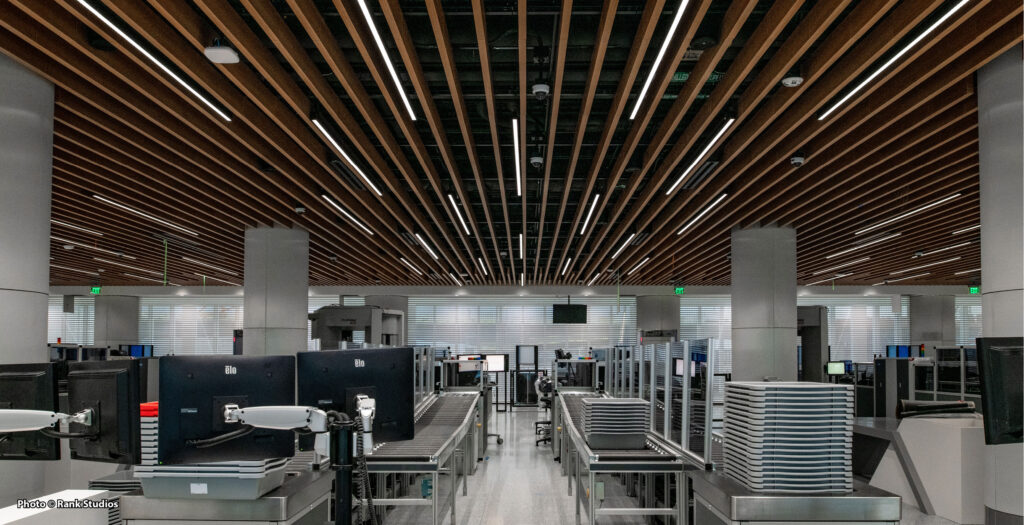
Cory Leonard: Recently at LAX (Los Angeles International Airport), our team performed as the Program Manager/Construction Manager on a major airline modernization program valued at $2.3 billion. This program entailed a lease agreement with the Airport Authority that required the airline to submit for design and construction reimbursement through a series of acquisition packages, all of which was orchestrated by our PM/CM team. To support this, we immersed ourselves in the airline’s internal accounting systems, reconfigured pre-existing project controls software, developed processes/procedures per Owner/Client requirements, managed supply chain costs/schedule, reported on performance, and prepared the acquisition packages for reimbursement. This was crucial in preventing delays in reimbursement and avoiding added interest costs. It takes detailed planning and tested experience to manage complex project budgets like these.
Lawrence Pitkin: It’s a credit to our team that we accelerated the construction schedule and supported multiple stakeholders.
Rigo Salinas: How does working in a constrained site such as an airport differ from other large infrastructure projects?
Jason Foley: Beyond the construction site itself, constrained storage is a major challenge. Applying phasing and logistics helps us schedule arrivals of concrete, conduits, pipes and determine which closures might impact transporting those materials to the site itself. With our unique software approach, we can assess how activities are developing to determine the best way forward.
Jonathan Clouser: You have to adopt a builder mentality. A logistics plan encompasses more than getting materials from point A to point B safely. Is it maximizing the customer experience? Can it be transported efficiently while maintaining FAA requirements? The easier our team makes it to bring in materials unencumbered, we can better avoid lost time and labor.
Rigo Salinas: What about the customer experience outside of the airport itself? We’ve all experienced the frustration of getting off your flight only to take a long and convoluted path to your car because of construction or navigating through construction detours.
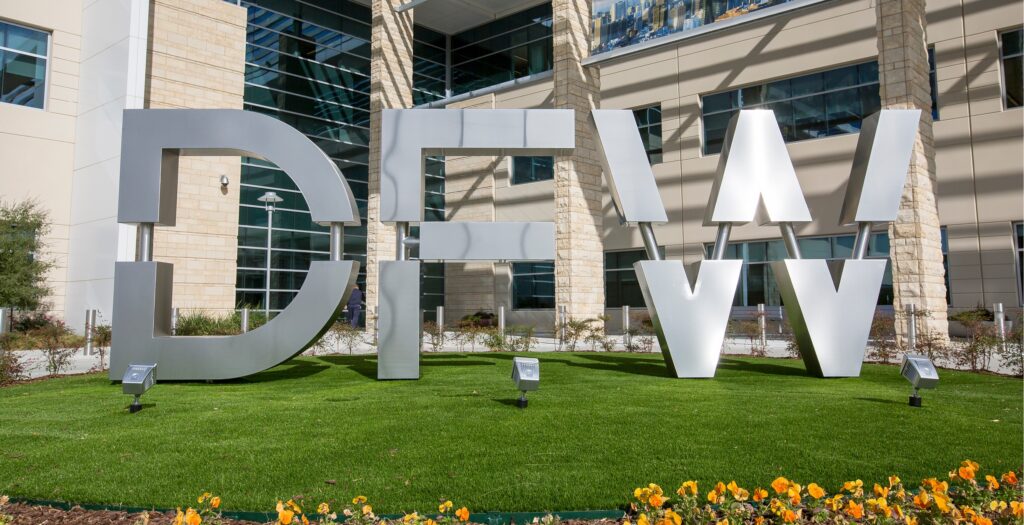
Patrick McCollom: That’s why we aim to “future-proof” our nation’s airports. To estimate and measure construction closures, impacts and future planned conditions, we conduct extensive modeling based on the changes and estimated passenger, vehicle or aircraft uses. At Dallas-Fort Worth International Airport, our work is supporting a major restoration to the International Parkway (IP Right), the biggest civil landside project in the airport’s history and the first civil design-build project. The new roadways will also need to be changed to be at-grade with the updated bridges, all while keeping the active airport in mind. To create minimal disruptions to airport users, our team is limiting roadway work to nights. When we talk about this improvement, it’s always about safety. Our goal is to achieve a level of predictability that improves the driving experience.
In Houston, we used similar practices to relocate the arrivals curb for Terminal B at Houston’s Bush Intercontinental Airport (IAH) to improve the customer journey. Understanding your traffic demands and modelling it with alternatives was crucial to the construction and final plan of this reconfigured Curbsides and Roadways.
Rigo Salinas: What have been some of your biggest takeaways from past aviation projects that you’re applying to the work you do now?
Jonathan Clouser: You have to leave room in the schedule to account for unexpected changes. Sometimes a bird’s nest or ad hoc wiring requires us to get creative to stay on schedule. With scheduling, it’s a balance of practicality, optimism, and experience.
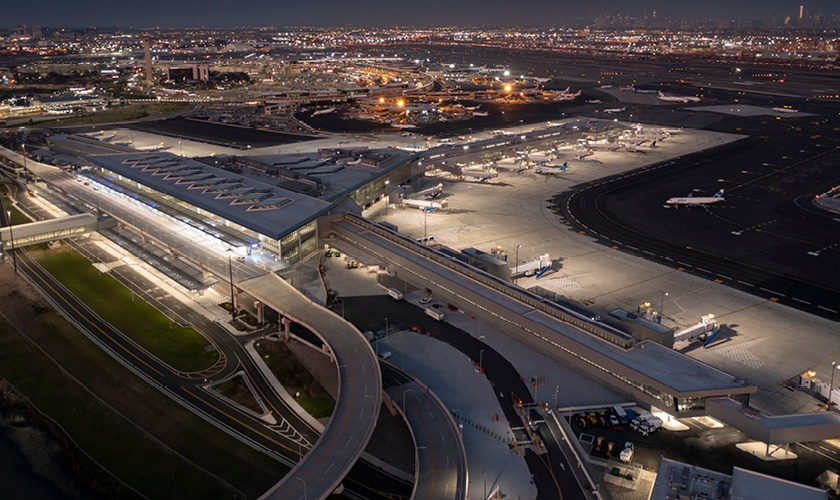
Jason Foley: We benefitted from creating a co-located team. In addition to our CM group and contractors, we asked designers and engineers to work onsite with us to address any given changes at a moment’s notice to maximize the timeline.
Dave Watson: Ultimately, our goal as CM is to act as stewards for the project and create internal redundances to provide the most accurate budget, cost controls, and advisory services on behalf of the client.
The STV leaders featured in this roundtable include Jonathan Clouser, project director; Jason Foley, project manager; Cory Leonard, project controls manager; Patrick McCollum, vice president, senior program manager; Lawrence Pitkin, senior project manager; Dave Watson, CCM, vice president, and West Region manager.
Read on for more about STV’s airport innovations and aviation portfolio.