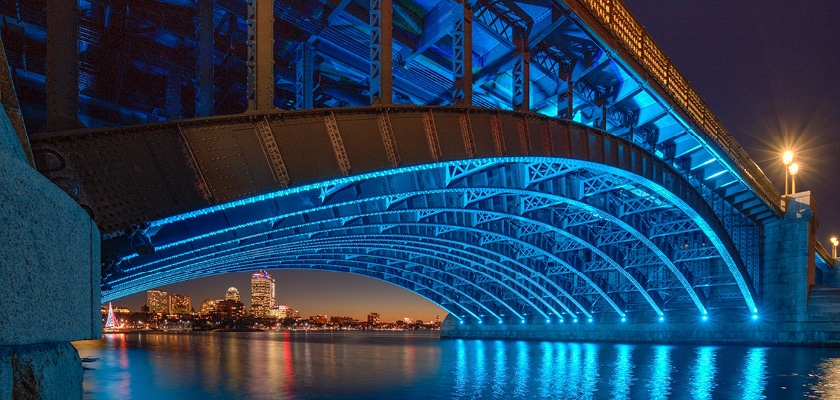
The Longfellow Bridge is not only an emblem for the Commonwealth of Massachusetts but also a crucial piece of infrastructure between Cambridge and Boston carrying Route 3 and the Massachusetts Bay Transportation Authority Red Line over the Charles River. The rehabilitation of the bridge, which first opened to traffic in 1907, is a significant milestone for the Commonwealth, while also serving as a key example of the delicate balancing act design and construction professionals must bring to a project like this as it relates to preserving history, while also enhancing structural performance to meet current codes.
As the lead designer as part of the design-build team that led the structure’s rehabilitation, our scope encompassed engineering and architectural designs for the complete reconstruction of the bridge’s original 11 open-spandrel steel arch spans and a 12th span that was installed in the 1950s; the seismic retrofit of 12 masonry substructures; and the reconstruction of the four signature “salt and pepper” 58-foot granite towers flanking the main span.
Construction phasing was an important aspect of the project, which was procured as part of the Massachusetts Department of Transportation’s Accelerated Bridge Program. The bridge carries 90,000 Red Line train passengers, 28,000 cars and trucks and well over 1,000 bicyclists and pedestrians daily between Boston and Cambridge, so the bridge needed to remain open during construction.
However, as we recently highlighted for a presentation to the Illinois Chapter of the Structural Engineers Association, the historic nature of the bridge presented design challenges, especially as it related to elements and detailing that was considered an essential part of the structure’s original character. For example, the Longfellow Bridge utilized hot riveting during its original construction in 1907. So, our team needed to develop a methodology and application for modern large-scale riveting of a historic and incredibly detailed structure, that also considered all local, state, and national requirements.
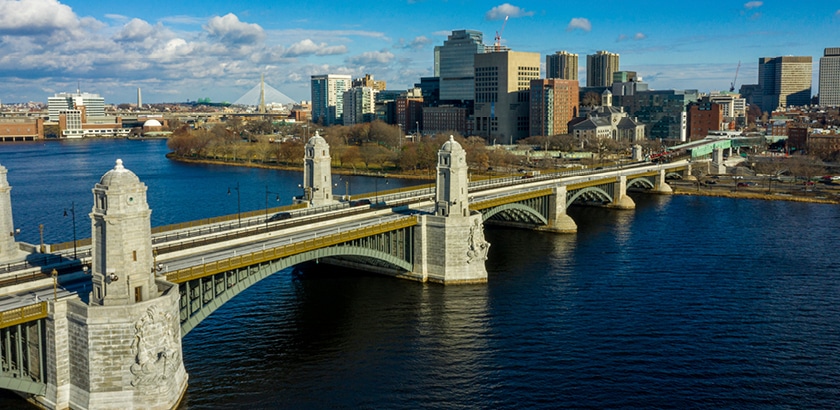
Upon a thorough inspection, it was determined that nearly the entire superstructure of the bridge – save the arch girder ribs – needed to be replaced as part of the program. However, to honor the bridge’s history, that meant the design needed to incorporate modern steel that replicated the original design and aesthetic. This included more than 2,600 lattice spandrel columns, the stringer-floorbeam system under the main roadway, sidewalk stringers and beams, and all of the floorbeams under the Red Line.
The more publicly visible the structural element, the more sensitive we were ensuring the finished project met historic preservation requirements. And the bulk of the most visible structural elements needed to be fabricated using riveting.
We knew early on that riveted construction came with its own set of challenges, such as identifying appropriate fabricators to perform the work, as well as QA/QC considerations regarding the constrained project area and the large size of some of the equipment needed for the operation. However, the further we got into the construction phase, the more challenges emerged, including limited availability of certain materials and a coatings issue on certain riveted members.
Our design called for a galvanized, mid-coat, top-coat system on the structural steel, including the existing columns we intended to reuse. To accomplish that, the existing columns were removed from the bridge, cleaned and repaired, and then galvanized before receiving an application of mid- and top coats. But in a matter of weeks, we noticed there was rust bleed near all the rivet holes where the galvanization couldn’t reach between the plies of built-up members, so we needed to replace all the original columns with members designed to be exact replicas.
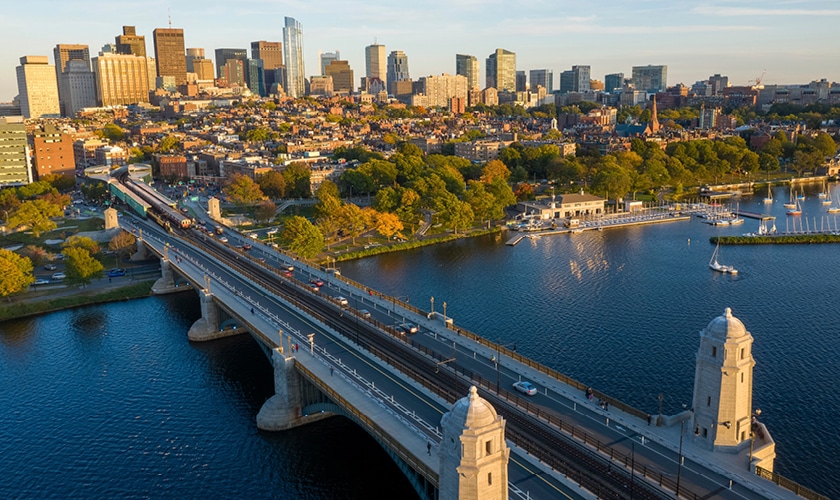
We encountered similar challenges when it came to replacing the Longfellow’s steel buckle plates. On the original bridge, steel buckle plates were used as structural members spanning between stringers to hold up the unreinforced concrete deck. As structural members, buckle plates have been obsolete since reinforced concrete was introduced, but from a historic restoration point of view, they were very important to the Longfellow’s rehabilitation. Our goal was to preserve as many buckle plates as possible. However, once demolition started, it became clear that all of the plates were in poor shape and could not be salvaged, so like the columns, we needed to design replica buckle plates to be fabricated and installed on the roadway.
For the proposed column-arch rib girder connections, we call for fastening a riveted column to the baseplate via tension control bolts. Once again, when the project was under construction, we had to adapt to unforeseen challenges. In this instance, the construction team couldn’t deploy the tools required because the original rivet connection was too close to the column base angle. Additionally, when removing the columns and baseplates from the arches, we found that the rivet holes through the arch flanges and plates were incoherently scattered all over the place. Some were oversized and in other instances, the holes between adjacent plies didn’t line up. So, we had to adjust our design to connect the structure’s arches to its floorbeams.
Approximately 10,000 structural rivets were used for this project, but the design-build team was successful in maintaining the historic fabric of the majestic bridge, while also connecting the cities of Boston and Cambridge with a modern structure that serves the needs of motorists, transit, pedestrians, cyclists and more. The project has received a series of awards, including the Abba G. Lichtenstein Medal from the 2020 International Bridge Conference, the 2019 Preservation Achievement Award by Boston Preservation Alliance and the 2019 Public Works Award from the American Public Works Association.
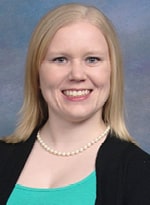
Heather Moulton, P.E., is a structural engineer and was a structural designer for the Longfellow Bridge Rehabilitation project. She has more than 10 years of experience supporting the design of bridges, rail stations and other transportation infrastructure.
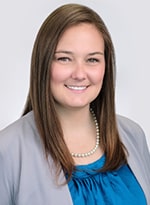
Alison Love, S.E., is a structural engineer and was a structural designer for the Longfellow Bridge Rehabilitation project. She has more than 10 years of experience developing designs for concrete and steel structures.