As the largest rapid transit yard in MTA New York City Transit’s (NYC Transit) subway system, as well as one of the largest yards of its kind in North America, the Coney Island Yard complex in Brooklyn, NY, is a vital piece of infrastructure for the nation’s busiest transit system.
During Superstorm Sandy in 2012, the complex was inundated with over 27 million gallons of saltwater and debris from nearby Coney Island Creek, causing significant damage to 28 different structures within the yard including maintenance shops, and disrupting the subway system’s core capacity for repairs.
In Sandy’s immediate aftermath, STV was tapped by NYC Transit to help the agency restore the complex’s vital maintenance capabilities. In just 11 weeks our team developed an emergency, short-term solution to protect the site at the 100-year flood-level, effectively resolving the immediate vulnerability after a brief six-month construction phase.
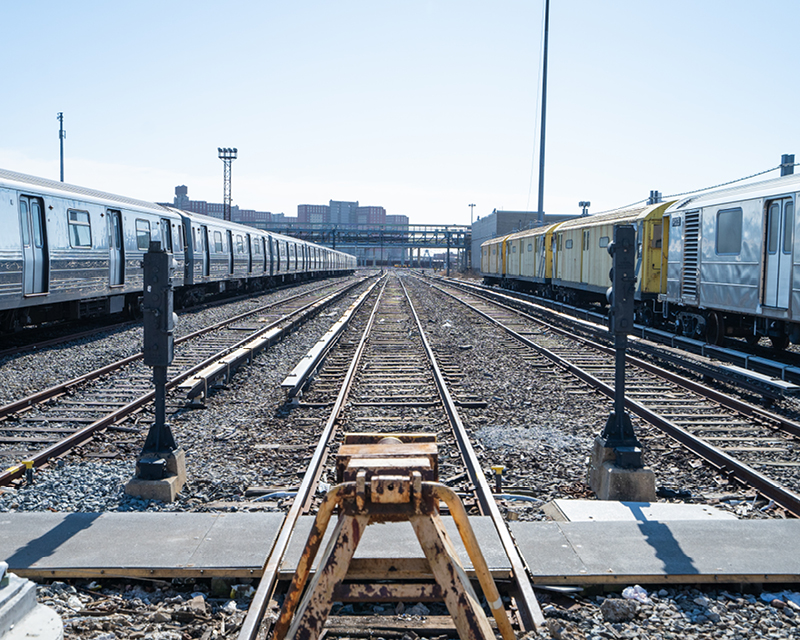
To create a long-term solution, NYC Transit initiated a multifaceted plan to create an even more resilient Coney Island Yard complex, including a robust perimeter protection system, featuring a 12,000-linear-foot-long, 15-foot-high flood wall with a 30-foot-deep cutoff wall designed to protect against a SLOSH Category 2 model storm event with additional freeboard, along with numerous drainage and power resilience improvements. Our team, in partnership with NYC Transit and MTA Construction & Development, provided a full suite of advisory, planning and design services to support this endeavor.
The success of the Coney Island Yard resilience transformation stands as an amazing example of innovation, interdisciplinary collaboration, clear communication and cohesive teamwork. Early on, when we were conducting our damage review and feasibility study to pinpoint viable flood mitigation solutions, the challenge of the program became apparent – especially as it related to securing the perimeter of the complex in both the short and long terms, all performed while ensuring the functionality of an active rail yard.
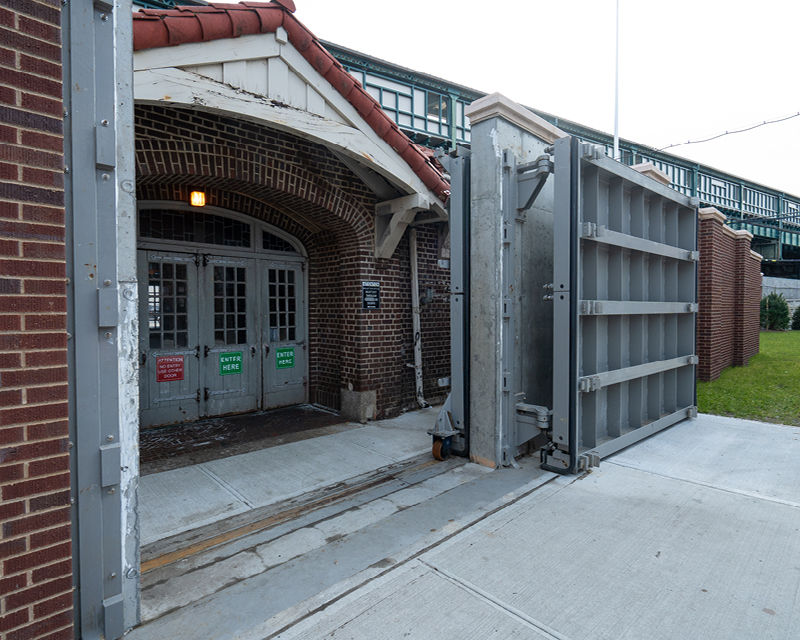
Following the implementation of short-term improvements, our team developed a permanent barrier, access and drainage systems for the complex. The final long-term flood wall, designed for a significant future coastal storm, combines sheet piles and concrete walls for structural security. The complex features eight large-scale sliding structural steel custom vehicular flood gates and a pedestrian access gate.
The Traction Motor Shop, a crucial building in the complex, underwent extensive hardening on two sides to tie it into the perimeter barrier. The hardening effort included delicately rebuilding pieces of the historic façade and creating a new rapidly deployed flood and security barrier for the many ventilation louvers. Our team coordinated with the barrier’s manufacturer to develop a roll-down security gate that was fully equipped with segmental aluminum flood planks to meet the required flood loads and debris impacts.
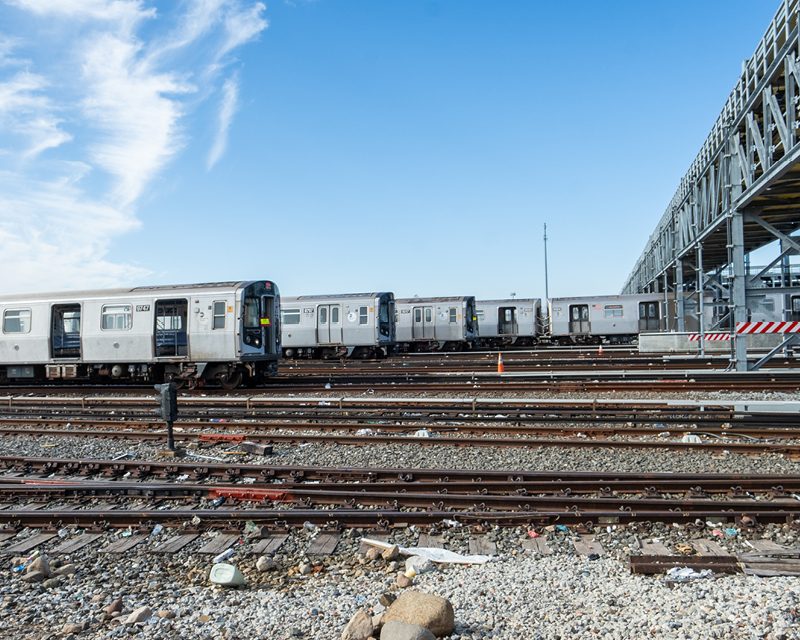
In addition to the perimeter barrier, the long-term protection features significant improvements to the interior drainage system, which mitigates the bathtub effect during heavy rainfall. Two additional pumping pits were put in place to handle storm surge conditions. The yard now efficiently drains by gravity to Coney Island Creek, ensuring dry conditions for the design 24-hour rainfall in non-storm surge situations. In storm surge conditions, two pump stations, comprised of three 3,000 GPM portable pumps each, can be activated to push against the exterior surge waters to maintain a mostly dry yard even coupled with heavy rainfall. In all, there are 10,000 linear feet of new underdrain pipes and 1,500 linear feet of replaced pipes. The extended construction team strategically managed the schedule to minimize train disruptions, highlighting proactive coordination between all stakeholders.
Another pivotal element of the project involved restoring and replacing damaged power infrastructure. Our team’s comprehensive site assessment revealed damaged and salt water-contaminated cables, corroded DC disconnect switches and deterioration in manholes and negative bus bars. Additionally, positive cables were inactive due to faults, and duct banks had collapsed. STV conducted a cost benefit analysis to compare the expenses of constructing a new above-track cable bridge versus new underground duct banks. The team collaborated with yard operations staff to assess the operational impact of the two proposed design solutions and, following these evaluations, NYC Transit opted for the above-ground solution to minimize disruption and maximize future protection.
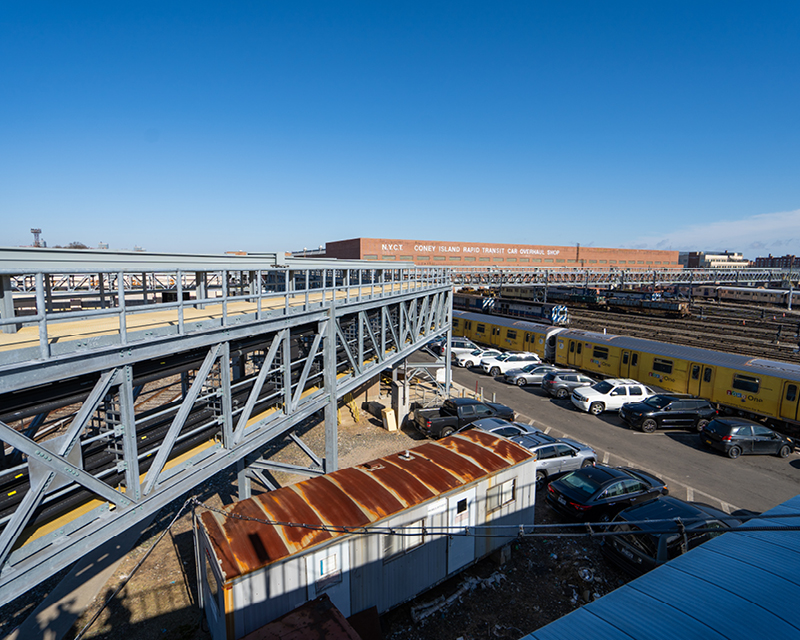
The Coney Island Yard Cable Bridge, a 4,000-linear-feet elevated cable system within a structural steel box truss, efficiently supports personnel as well as traction power and communication infrastructure. Fabricated off-site and constructed in large segments, its installation minimized operational disruptions and enhanced construction efficiency.
The above-ground cable bridge solution allowed the construction of an entirely new traction power distribution system with little to no impact on the existing system. Additionally, once construction of the new system neared completion it was an easy transition from old to new.
This was an innovative project for both STV and NYC Transit and we are all proud of our partnership to develop a solution that will serve the riders of this transit system for generations to come. This large investment into hardening the city’s critical transportation infrastructure is paid off by the even larger economic and social gain from the city’s resilience to current and future storms.